The drilling press was modified by a previous owner. As it can be seen in the picture below, someone added an intermediate pulley in the driving train to reduce the rotation speeds. What was the motor pulley became the intermediate pulley and a new single step pulley was fitted to the motor shaft. I have some doubts about the origin of this variation: would it be made at the Wörner factory after a specific requirement by a client?
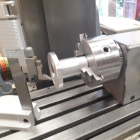